As a building owner in the great state of Texas, ensuring the smooth functioning of your property’s mechanical, electrical, and plumbing (MEP) systems is crucial for the overall efficiency and longevity of your investment. The commissioning and testing of MEP equipment play a pivotal role in achieving this goal. In this article, we will explore the nine best steps to commission and test MEP equipment, providing practical insights tailored to the specific needs of building owners in Texas.
Table of Contents
Step 1: Develop a Comprehensive Commissioning Plan
The first and foremost step in the process is to create a detailed commissioning plan. This plan should outline the scope, objectives, and schedule for commissioning MEP equipment. Collaborate with qualified professionals, such as engineers and contractors, to ensure that the plan aligns with local building codes and regulations in Texas. A well-structured commissioning plan serves as a roadmap for the entire process, fostering a systematic approach.
Step 2: Hire Qualified MEP Professionals
Invest in hiring qualified MEP professionals who have a deep understanding of the unique challenges posed by the Texas climate. Ensure that the professionals you choose are licensed and experienced in working with MEP systems in the region. Their expertise will prove invaluable in identifying potential issues, conducting thorough testing, and recommending optimal solutions for your specific building requirements.
Step 3: Conduct Preliminary Design Reviews
Before the actual installation of MEP equipment begins, conduct preliminary design reviews to identify any potential flaws or discrepancies in the plans. This proactive approach helps in addressing issues at an early stage, preventing costly delays and rework later in the process. Engage with your design and construction teams to ensure that the proposed designs align with the intended functionality and efficiency goals for your Texas property.
Step 4: Implement Stringent Quality Control Measures
Quality control is paramount in the commissioning and testing of MEP equipment. Implement stringent measures to verify that the installed equipment meets the specified standards and complies with local regulations in Texas. Regular inspections, material testing, and adherence to industry best practices will contribute to the overall reliability and longevity of the MEP systems in your building.
Step 5: Perform System Verification Tests
Once the MEP equipment is installed, it’s time to conduct system verification tests. These tests evaluate the performance of individual components as well as the integrated MEP systems. Focus on aspects such as heating, ventilation, air conditioning (HVAC), electrical distribution, and plumbing. System verification tests help in identifying any operational issues and ensure that the MEP systems function seamlessly in the Texas climate.
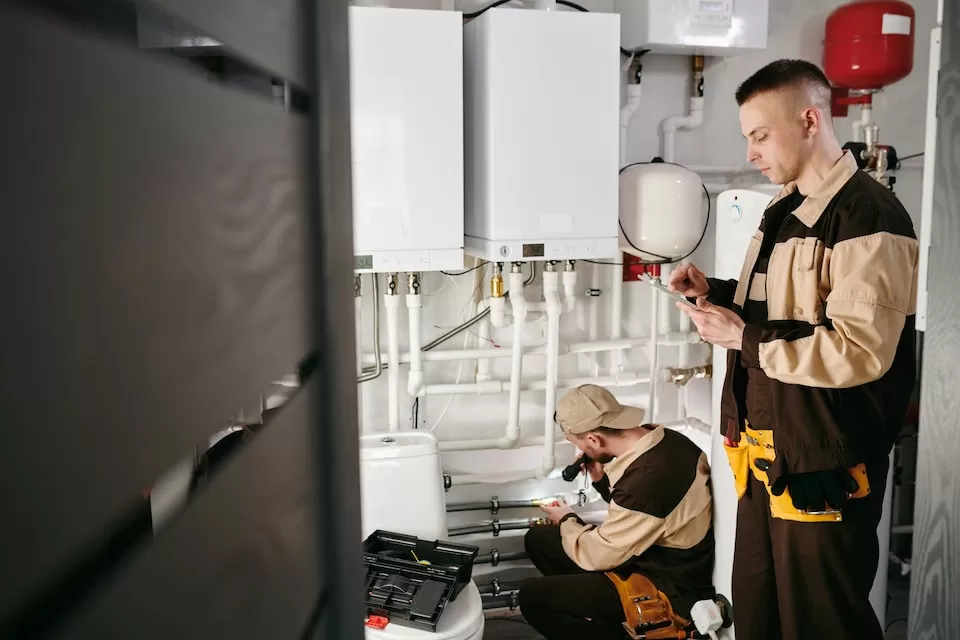
Step 6: Simulate Real-World Conditions
To accurately assess the performance of MEP equipment, simulate real-world conditions that the systems will encounter during their operational life. This includes variations in temperature, humidity, and load conditions. By subjecting the systems to realistic scenarios, you can uncover potential weaknesses and fine-tune the MEP equipment to perform optimally in the diverse climate conditions experienced in different regions of Texas.
Step 7: Document and Analyze Test Results
Thorough documentation and analysis of test results are critical steps in the commissioning process. Create a comprehensive record of all tests conducted, including detailed observations and measurements. Analyze the results to identify any deviations from expected performance standards. This documentation serves as a valuable reference for future maintenance and troubleshooting, contributing to the long-term success of your MEP systems in Texas.
Step 8: Address Identified Issues Promptly
During the testing phase, it’s not uncommon to uncover issues or deficiencies in the MEP equipment. Addressing these issues promptly is essential to ensure the functionality and safety of your building. Collaborate with your MEP professionals to develop effective solutions and implement necessary adjustments. Proactive problem-solving will mitigate potential risks and contribute to the overall resilience of your building’s MEP systems.
Step 9: Implement Ongoing Maintenance Protocols
Commissioning and testing are not one-time activities; they are integral components of an ongoing maintenance strategy. Develop and implement protocols for regular inspections, preventive maintenance, and system optimization. Establish a partnership with local service providers in Texas who specialize in MEP maintenance to ensure that your systems continue to operate efficiently throughout their lifecycle.
Conclusion
In conclusion, commissioning and testing MEP equipment for building owners in Texas require a meticulous and strategic approach. By following the nine Steps to Commission and Test MEP Equipment, you can enhance the reliability, efficiency, and longevity of your building’s mechanical, electrical, and plumbing systems. From developing a comprehensive commissioning plan to implementing ongoing maintenance protocols, each step contributes to the overall success of your investment in the vibrant and diverse landscape of Texas. Remember, a well-commissioned and tested MEP system is not just a necessity; it’s a key factor in the sustained success of your property in the Lone Star State.